Questo piccolo articolo divulgativo mi fu commissionato dopo la tesi di laurea per una pubblicazione su una rivista tecnica, per fare un primo punto sulle tecnologie di scansione esistenti, circa venti anni fa. Mentre per gli operatori del settore tutto cio’ era gia’ ben noto, il grosso pubblico, anche professionale, era piuttosto all’oscuro sulle potenzialita’ e sulle tecnologie disponibili. Per cui fu una bella idea da parte del dipartimento del Politecnico di buttare giu’ qualche riga e creare una panoramica.
Bisogna dire che a livello di tecnologie, da allora non e’ cambiato essenzialmente nulla ( al contrario delle manifatture additive che hanno moltiplicato le tecniche ) : quello che e’ cambiato sono essenzialmente la risoluzione, la accuratezza e la velocita’ dei sistemi, nonche’ la maneggevolezza e soprattutto i costi, che sono diventati abbordabili per aziende anche di piccola – media dimensione. Naturalmente anche il software di gestione e’ cambiato moltissimo, e questo fa veramente la differenza: a mio personale giudizio, il 70-80% della qualita’ della scansione e del risultato finale risiede proprio nel programma a corredo, e per questo si consiglia sempre di valutarlo in prova se possibile. I soli dati di targa di uno scanner, di per se’, non dicono piu’ di tanto quando si fa un confronto prima dell’acquisto.
Molte specifiche tecniche sono talmente cambiate che non e’ piu’ il caso di riportarle, ma resta valido il nucleo introduttivo e i campi di applicazione. Lasciamo le vecchie immagini.
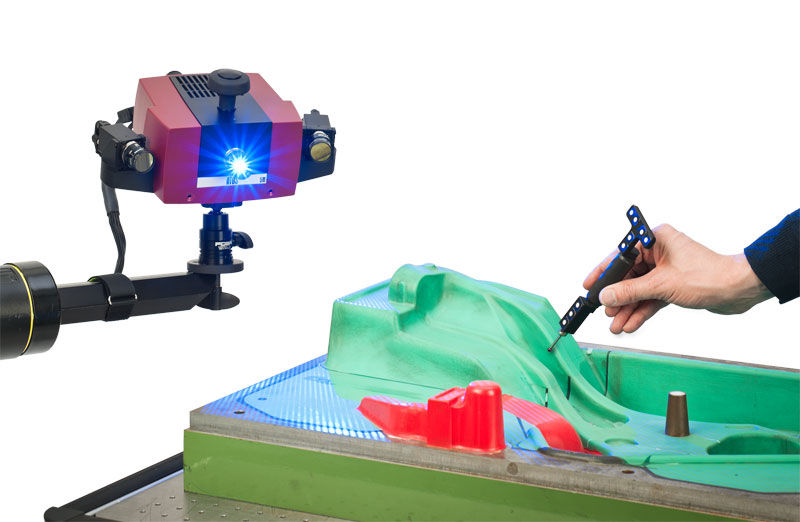
Introduzione
La “reverse engineering” (RE) o “ingegneria inversa” è il processo di creazione di un modello tridimensionale ottenuto misurando un oggetto da riprogettare o modificare, per determinarne dimensioni e tolleranze quando non si abbiano a disposizione dati dimensionali specifici. Il termine include quindi ogni attività compiuta per determinare forma e funzione di un oggetto o per comprendere le idee e la tecnologia alla base del processo di produzione. Una diversa definizione è quella che indica la RE come il processo tramite il quale tutte le informazioni che non possono essere immediatamente ottenibili (quote, curvature, ecc.) sono estratte tramite un’ apposita attrezzature e convertite in un formato direttamente interpretabile, quale un modello CAD, per essere manipolate o duplicate.
La reverse engineering è il metodo di studio ideale da usare nelle seguenti situazioni:
- non esistono disegni di un modello fisico di un prodotto (caso molto frequente con prototipi o prodotti artigianali);
- sono stati creati i disegni, ma i prototipi utilizzati nella lavorazione sono stati modificati;
- si necessita di un processo di riprogettazione, come nel caso di sviluppo di nuovi prodotti;
- un nuovo sistema CAD è stato introdotto nell’azienda, e tutti i dati dei prodotti esistenti devono essere caricati nel nuovo sistema;
- si vuole comprendere il funzionamento di un prodotto esistente sul mercato, ponendo attenzione al rispetto del brevetto;
- tutti i dati posseduti dall’azienda di un prodotto finito sono andati perduti.
Questa tecnica può essere realizzata attraverso un’ampia varietà di sistemi e tecnologie che, differiscono per velocità, precisione e dimensioni del volume di lavoro. La possibilità di scegliere il modello che più si adatta alle proprie esigenze è oggi sicuramente ampia e diversificata, sia in termini di prestazioni che di costi, ma proprio questo aspetto causa una notevole frammentarietà del mercato ed una conseguente difficoltà di scelta del sistema ottimale.
Tecnologie di acquisizione
Attualmente il mercato dei sistemi di reverse engineering raccoglie due principali famiglie di sistemi: quelli a contatto e quelli senza contatto.
Sistemi a contatto: sono costituiti dai tastatori (touch probes) applicabili sulle macchine di misura o più raramente calettati sui mandrini delle macchine utensili. Per un uso nei reparti di modellistica o per rilevare pochi punti significativi, gli stessi tastatori sono montati su bracci articolati che garantiscono all’operatore una grande libertà di movimento ed eventuali problemi di posizionamento (occlusioni, sottosquadri). Questi accessori sono stati inseriti nei sistemi di scansione anche grazie alla possibilità di trascinamento del tastatore lungo la superficie, con precisione del micron.
Punti di forza di questi apparecchi risiedono nella grande precisione delle macchine di misura, se operanti in condizioni ambientali ottimali, nel costo moderato del solo tastatore, se si opera con una macchina preesistente, e nella flessibilità di raccolta dei dati, sia come libertà di percorso che come densità di punti rilevati. Per contro non è possibile operare con materiali teneri, esiste la possibilità di lasciare tracce su superfici delicate, e non è possibile rilevare parti con raggi di curvatura inferiori a quelle del tastatore.
- I sistemi a contatto trovano impiego nell’industria aeronautica per controllo qualitativo in genere di portelloni, finestrini, ali, timone, fusoliera, sedili, tubi; nell’industria automobilistica per rilevamento di superfici come portiere, parabrezza, finestrini, parti stampate o di fusione, sedili, mascherine, e genericamente nell’industria per pezzi ottenuti per fusione, stampati, sinterizzati, controllo di allineamento di pezzi saldati; verifica di superfici per individuazione di fori o altre discrepanze rispetto al sistema CAD; settore orafo, gioielleria, materiali vetrosi e cristalli, impossibili da scansionare con sistemi ottici. Da ricordare anche che nel campo dell’intrattenimento, sono particolarmente adatti per la scansione di personaggi ed oggetti di piccole dimensioni per la creazione di videogiochi e film.
Sistemi senza contatto: questa categoria raggruppa sia i sistemi ottici, a luce bianca o laser (da molti operatori definiti i soli strumenti per RE), sia acustici e magnetici. Tutti questi strumenti offrono il vantaggio di operare attraverso un processo automatico di rilievo dei punti: la limitazione della libertà di lavoro da parte dell’operatore è compensata da una maggiore densità di punti rilevati e da un maggiore controllo delle misure. Sono maggiormente indicati per superfici free-form e non si hanno problemi nel rilevamento di oggetti fragili o facilmente scalfibili. Peraltro presentano grosse difficoltà nel rilevare parti interne o nascoste, necessitano di un post-processamento manuale per l’eliminazione dei dati spuri e richiedono la ricostruzione manuale delle singole viste rilevate, giacché l’oggetto deve essere rilevato da più direzioni per ottenere la forma completa.
I sistemi a luce laser operano secondo tre modalità: gli scanner a triangolazione, di gran lunga i più diffusi per usi di piccole e medie dimensioni, sfruttano la riflessione del raggio laser contro la superficie dell’oggetto rilevando le coordinate per mezzo di un sensore. Le prestazioni arrivano al centesimo (vengono dichiarate precisioni micrometriche per apparecchi speciali). I sistemi possono essere indipendenti (stand-alone) o montati su una CMM.
Stesso principio, ma con una registrazione del tempo di percorrenza, anziché dell’angolo geometrico, è impiegato dai laser radar (time to flight laser scanner), mentre gli interferometri laser (laser trackers) sfruttano la differenza di fase di un raggio suddiviso all’origine. Questi ultimi due sono utilizzati in genere per distanze superiori ai precedenti; la precisione arriva al centesimo di millimetro con una velocità del raggio emesso di qualche metro al secondo.
- gli scanner trovano posto nel settore dei trasporti montati sulle macchine di misura per controllo della geometria di parti stampate, pezzi di fusione, superfici della carrozzeria; scansione di parti con geometria complessa, quali eliche navali; in impiantistica per rilevamento di parti di impianti nucleari, quali turbine o per manutenzione; è possibile utilizzare questi mezzi per creare simulazioni di realtà virtuale in cui vengono previste le modalità di intervento in situazioni pericolose per l’uomo, come interventi in esterno o a grandi altezze; in aeronautica per scansioni di parti complesse o gruppi meccanici, motori, turbine. Nell’industria per design, arredamento, rapid prototyping in generale, creazione di modelli interattivi per pubblicazione sul web e per filmati pubblicitari; creazione di modelli su misura di abiti, uniformi militari, abbigliamento e calzature sportive; oggetti casalinghi, gioielleria, allineamento di pavimentazioni, rivestimenti metallici; componenti stampati, fusi, ottenuti per elettroerosione; rilevamento di componenti elettronici e di computer: è d’uso creare una mappa tridimensionale del circuito una volta effettuato il montaggio, riuscendo a rilevare con esattezza il corretto assemblaggio e la planarità, oppure per rilevare parti danneggiate. Ancora ricordiamo il campo dei beni artistici, dove la possibilità di sfruttare sistemi a colori (RGB laser) rende possibile la catalogazione degli oggetti con colori originali, ed il campo medico ricostruzione di parti cartilaginee, superfici interne con tessuti molli come faringe, apparato digestivo; ortopedia, in modo particolare scansioni dell’intero piede per calzature; protesi d’anca, tecnica degli impianti dentaria; rilievo di superfici esterne con bassissime asperità, quali superfici dentarie, pelle, valvole cardiache.
- Gli interferometri e i laser radar trovano posto nella scansione di edifici storici di qualsiasi dimensione (palazzi, cattedrali, rovine, ecc.), immagini complete di raffinerie, capannoni, hangar, serbatoi, silos, impianti chimici, piattaforme petrolifere; ponti, cave, viadotti autostradali; modellizzazione di scafi di navi, sommergibili, superfici alari. In industria per l’allineamento di componenti, posizionamento di robot, controllo qualitativo in generale; misure di laboratorio.
Gli altri sistemi ottici comprendono le tecniche sfruttanti la luce bianca: molto diffusi per le prestazioni e per la maneggevolezza sono gli apparecchi a luce strutturata (structured light), sfruttanti fenomeni di frange interferometriche proiettate sull’oggetto da rilevare, che si contendono con gli apparecchi laser il dominio del mercato industriale. La luce bianca è naturalmente il principio di base anche dai sistemi utilizzanti apparecchi fotografici. Con essi si è in grado di fornire una ricostruzione tridimensionale di oggetti o ambienti con tempi di acquisizione pressoché istantanei tramite appositi software in grado di assemblare le viste dell’oggetto catturata da differenti angolazioni; il campi di lavoro arriva mediamente fino a 10 metri di diametro senza una sostanziale perdita di definizione. L’ultimo ritrovato di sistema a luce bianca è rappresentato dall’olografia conoscopica, il quale utilizza una fonti di luce non coerente e con precisione assolutamente ragguardevole (ordine del micron). Il campo di lavoro è peraltro limitato ad oggetti di piccole dimensioni.
- nel settore industriale gli apparecchi a luce strutturata sono impiegati per possibilità di video-catalogazione di oggetti prodotti in numerosi modelli (occhiali, abiti, orologi, ecc.) e di creazioni nel settore cosmetico (acconciature, make-up, ecc.); creazioni personalizzate di abiti, uniformi per l’esercito, divise; nel campo dell’automotive per reverse engineering di stampi di particolari per confronto con disegni CAD, rilevamento di particolari di forma complessa o dell’intero veicolo, superfici con fori e spigoli vivi non rilevabili con altri sistemi ottici, in avionica per . controllo qualitativo dell’intera superficie esterna; rilevamento per analisi CAD, FEM. In medicina recenti usi in telemedicina, applicazione in chirurgia plastica ed estetica, in podologia, e anche scansioni a 360° per l’applicazione di busti ortopedici. L’applicazione più avanzata rimane quella della scansione dell’intero campo operatorio per creare un ambiente chirurgico virtuale a scopo di insegnamento. Per ultimo citiamo una delle ultime frontiere, quella del settore legale, con l’ archiviazione di profili di criminali, con un grado di dettaglio decisamente superiore a quella fornita dalle fotografie e confronto dei soggetti con immagini registrate da videocamere di sicurezza.
- La fotogrammetria trova ampio spazio in aeronautica eliminazione dell’uso dei calibri per lavorazioni su macchine utensili; realizzazione di modelli CAD in grado di eliminare costosi modelli, soggetti a deterioramento; reverse engineering per produzione di componenti da parte di ditte esterne; modellizzazione di parti interne, come cabine di pilotaggio, reparto passeggeri, ecc; montaggio e controllo di moduli spaziali. Ancora per interni di mezzi terrestri, rapid prototyping, comparazione di volti ricostruiti prima e dopo l’intervento chirurgico; ricostruzioni mammarie con confronto della protesi da applicare con la parte sopravvissuta.
Le ultime categorie di prodotti riguardano: i sistemi ad ultrasuoni, sia portatili che industriali, basati sul tempo di riflessione delle onde sonore: sono apparecchi a basso costo, ma fortemente soggetti a disturbi ambientali; sistemi ad emissione magnetica, per cui valgono le medesime considerazioni, e l’uso della tomografia per uso industriale, dove l’emissione di raggi X rende possibile visionare anche l’interno dell’oggetto in studio. Questi sistemi, peraltro poco diffusi, hanno risoluzioni inferiori ai precedenti.
- I sistemi ad ultrasuoni ed emissione magnetica trovano posto in parecchi settori industriali, anche se lo scopo primario resta quello della tecnica ispettiva;
- la tomografia, oltre ad essere tradizionalmente adoperata in campo medico anche per avere modelli tridimensionali per pratiche ricostruttive, è anche rintracciabile in meccanica per scansioni interne, controllo qualitativo, ricerca di difettosità di qualunque componente meccanico o macchine quali motori, pompe, ecc.
Riportiamo in ultimo una immagine riepilogativa che collega i sistemi ai campi di applicazione:
Criteri di scelta
Conseguentemente ogni qualvolta sia interesse di una società scegliere il sistema di acquisizione più opportuno per la sua realtà produttiva, sarà necessario effettuare alcune valutazioni preliminari per non incorrere in errate acquisizioni, legate all’utilizzo, al campo di applicazione, alle condizioni ambientali ed ai costi.
I parametri che vengono considerati in questa prima fase di cernita possono essere riassunti nei punti seguenti:
- dimensioni dell’oggetto: i sistemi variano a seconda del volume di lavoro, cioè dello spazio misurabile, spaziando da pochi centimetri alle centinaia di metri. E’ perciò inutile acquistare un sistema laser a tempo di riflessione, normalmente impiegato per la rilevazione di edifici civili, per la progettazione e produzione di particolari meccanici. Ciononostante risulta importante scegliere uno strumento non troppo rigido, sempre in termini di volume di lavoro in cui si opera, poiché lo strumento acquisito sia sempre in grado di essere applicabile alla realtà produttiva nella quale viene introdotto. Qualora si operi con oggetti di dimensione ragguardevole e di difficile trasportabilità, è da valutare inoltre la possibilità di portare l’apparecchio presso l’oggetto al fine di renderne possibile la rilevazione.
- natura dell’oggetto: alcuni sistemi non risultano idonei al tipo di materiale d’impiego: è impossibile usare un laser con materiali vetrosi o molto riflettenti, a meno di coprire la parte con vernici opacizzanti, operazione spesso sconsigliata;
- precisione richiesta: più aumenta il volume digitalizzato, minore risulta la precisione. Controllare sempre il valore ottenibile dichiarato in base alle richieste, che variano notevolmente secondo l’ambito in cui operiamo: è chiaro che la precisione richiesta per realizzare un personaggio cinematografico o per una simulazione animata è decisamente inferiore a quella richiesta per un processo di ispezione e confronto in ambiente industriale. Se quindi la precisione richiesta è di x, i punti devono essere presi ad una distanza non superiore a x: questo può risultare un vincolo significativo quando si voglia operare con strumenti di acquisizione manuale, vedi braccetti antropomorfi, che non permettono l’impostazione di griglie di scansione prefissate;
- ambiente di lavoro: non sempre l’ambiente in cui si opera risulta idoneo al tipo di macchina scelta: l’eccessiva illuminazione può compromettere l’utilizzo di un sistema fotografico o laser, l’eccessivo rumore può disturbare un attrezzatura ultrasonica per ispezione, e così via, per cui occorre essere ben informati dal produttore su tutte le fonti di disturbo e sulle condizioni climatiche in cui la macchina può operare. Non va infine trascurato che alcuni sistemi richiedono un certo spazio di manovra attorno all’oggetto quale vincolo per una corretta focalizzazione del sistema;
- caratteristiche tecniche, costi e assistenza: individuato il sistema idoneo, è opportuno informarsi sui modelli presenti sul mercato non soltanto per confrontare prezzi e caratteristiche, ma anche allo scopo di valutare la disponibilità per servizio di assistenza e manutenzione. Molte ditte, infatti, hanno sede solo nel paese di origine o in zone geograficamente limitate, per cui l’acquisto di un prodotto da questi o da un semplice rivenditore locale può risultare oneroso, sia in termini di tempo che di costi, in caso di sostituzione, riparazione o calibrazione dei componenti.